Case Study – Compiled by FireRescue1.com/EMS1.com
MagneGrip • April 29, 2020
BACKGROUND:
The Dyersburg Fire Department in Tennessee is a full-paid agency with 50 sworn firefighters and three stations, providing EMS/Rescue coverage as well as primary fire response to a population of approximately 15,000 residents, with a 15.1 square mile service area which also encompasses part of an interstate, a regional airport, and a hospital. It is additionally an ISO Class 3 agency.
CHALLENGE:
As with many agencies across the country, Captain Rusty Hilliard says Dyersburg’s stations share common space between the apparatus bays and equipment storage. While it’s true that having both so close together could arguably make for a quicker response, it often comes down to a matter of limited room within the station house, especially for older stations built for much smaller vehicles than those used in modern firefighting.
One side effect of this arrangement, however, is the fact that diesel engines tend to produce not only a lot of fumes, but also the phenomenon known as “diesel dust,” a black particulate residue composed mainly of carbon that seems to settle and accumulate on anything it touches.
Capt. Hilliard says that for his department, that meant that sooty layers regularly accumulated on walls, bunker gear, SCBA equipment, and anything else in close proximity to the apparatus bays — including making its way, along with engine fumes, into crew living quarters nearby.
This problem was exacerbated by the constant egress and return of apparatus to and from calls, meaning that the engines were spending a fair amount of time running while within the bays’ relatively closed environment (even with the doors open, ventilation was not optimal to exhaust the fumes).
In addition to the health concerns caused by having carbon dust and diesel fumes flying through the air at a given moment, these two problems were also causing the agency to have to spend a lot of time and money working on keeping their equipment clean and in working order.
The final straw, however, came when the agency switched to a smoking-free environment in the quarters. Very shortly after cleaning the walls of the living quarters thoroughly, the crews noticed a not-insignificant buildup of diesel dust on the walls. Capt. Hilliard says this was the moment when the department knew it had to remedy the problem.
SOLUTION:
After looking through many of the options available on the market for exhaust handling and filtration, Dyersburg settled on the MagneGrip/AirHAWK combination system from MagneGrip, an ISO 9001:2008 Certified company. The system combines a NFPA 1500-compliant vehicle exhaust system (MagneGrip) with a self-sealing nozzle, and a 4-stage filtration system (AirHAWK). The AirHAWK units are ETL/UL Certified and utilize advanced filtration such as photo-catalytic oxidation, which was developed by the Department of Defense to destroy toxic organic compounds.
Since the MagneGrip and AirHAWK have many different models and configurations (for example, in how the exhaust hoses are mounted), MagneGrip came out on-site to Capt. Hilliard to determine which system was the best fit for each of their three stations, and then custom-designed the components to match the specific needs of each apparatus.
RESULTS:
Almost instantly, Capt. Hilliard says, the crews noticed that the smell of the exhaust was completely gone throughout the station. Perhaps similar to going from a crowded city with a lot of cars to the countryside with far fewer, sometimes those who live with pollution don’t realize how much there is until it’s no longer present.
Maintenance time on cleaning the equipment, bays, and living quarters has drastically decreased due to the removal of the diesel dust from the ambient air, and the crews have reported much better conditions in the quarters as well.
In today’s era of reduced budgets, Hilliard notes, departments have to be careful what they invest in. He credits Chief Robert Veal, Jr. with having the foresight to realize that purchasing the MagneGrip/AirHAWK system would actually help reduce equipment costs in the long run including maintenance and replacement costs for items contaminated by the exhaust output.
More importantly, however, he realizes that the health, welfare, and job performance of firefighters depends on their ability to remain physically fit and ready, with fully functioning equipment. In these respects, Capt. Hilliard says, the MagneGrip/AirHAWK system has performed exceptionally.
FOR MORE INFORMATION OR BUDGETARY PROPOSAL:
www.magnegrip.com info@magnegrip.com 800-875-5440
Congratulations to all Firehouse Station Design Awards winners , especially our MagneGrip Exhaust Removal Systems and AirHAWK Air Purification Systems customers: Londonderry (NH) Fire Central Station, Long Hill Fire District (Trumbull, CT) Station #2, Urbandale (IA) Fire Station #43, Lake Travis Fire Station #606 (Austin, TX), City of Meridian (ID) Fire Station #6, North Ridgeville (OH) Fire Station #1, Tavares (FL) Public Safety Complex, Pearland (TX) Fire Station #1, Borger (TX) Fire Station, Maryland Heights (MO) Fire Protection District. Great looking facilities and kudos for keeping the health and well-being of your first responders top of mind.
In the past, fire stations built after 2003 were not eligible to apply for an exhaust removal system through AFG. This is no longer the case. Any fire department no matter the age can apply for an exhaust removal system through the AFG program. The only restriction is that the funds cannot be used for new construction projects. This is an important opportunity for fire stations and applies to the upcoming FY 2020 grants. Contact us for more information.
With colder temperatures and winter coming, first responders may be forced to spend more time inside the firehouse. And as concern about the spread of Covid-19 continues, many fire departments are looking at air cleaning and filtration in addition to CDC best practices of social distancing, mask wearing, handwashing and disinfecting. When used along with other coronavirus safety measures, air filtration can be part of a plan to protect fire responders indoors. According to CDC, “portable air cleaners (also known as air purifiers) may be particularly helpful when additional ventilation with outdoor air is not possible without compromising indoor comfort (temperature or humidity), or when outdoor air pollution is high. Air cleaners and HVAC filters are designed to filter pollutants or contaminants out of the air that passes through them. Air cleaning and filtration can help reduce airborne contaminants, including particles containing viruses.” For fire departments, AirHAWK Air Purification Systems offer air filtration units for various fire house areas including living space, sleeping quarters, office space, turnout rooms and apparatus bays. The portable AirHAWK 265 uses a multi-stage filtration process to remove contaminants and return clean, purified air back into the space. Each unit has a HEPA filter, photo-catalytic oxidizer to destroy toxic compounds and UL light to kill viruses and bacteria in addition to prefilters and gas absorption layers. AirHAWK 1000 is a ducted system and is the most efficient technology for moving pollutants into-and-through an air cleaning system rapidly. With a four-stage air purification system, AirHAWK 1000 is designed to provide an optimal air flow pattern that delivers maximum effectiveness in air purification. AirHAWK 3000 XL is designed for apparatus bay areas to remove particulates, toxic gases and other airborne contaminants found in diesel exhaust. Polluted air passes through AirHAWK’s four-stage filtration process to remove harmful substances. Clean, purified air is then evenly dispersed back into the facility. For more information about AirHAWK Air Purification Systems, go to www.magnegrip.com or call 800-875-5440.
MagneGrip, a manufacturer of vehicle exhaust removal and air purification systems, is proud to announce its certification as a Women’s Business Enterprise (WBE) and a Woman Owned Small Business (WOSB). This certification comes after Maggie Rossman-Roach succeeded her father, Edward J. Rossman, as President of the family-owned company in August 2018. In addition to Ms. Rossman-Roach, the company’s woman-owned management team includes Irma Rossman and Jennifer Rossman. “Earning our WBE and WOSB certifications is an exciting opportunity,” said Ms. Rossman-Roach. “It gives us the ability to support our clients in their commitment to supplier diversity while we continue to deliver exceptional products and service to reduce the risk of cancer in firehouses and vehicle maintenance facilities.” “Our certification is humbling recognition, not only for me and our sales, service and management team, but especially my father who founded the company. We all share in this milestone accomplishment.” MagneGrip was certified by the Women’s Business Enterprise Council Ohio River Valley (WBECORV), a regional partner organization of the Women’s Enterprise National Council (WBENC), utilizing WBENC’s national standard of certification. The process is rigorous and includes a comprehensive review of the business to confirm it is woman-owned, operated and controlled. About MagneGrip MagneGrip was founded in 1975 to provide air purification equipment and exhaust removal systems. Based in Cincinnati, Ohio, MagneGrip manufactures the #1-rated solution to the health threat of diesel exhaust emissions in firehouses and vehicle maintenance facilities. MagneGrip engineers, manufactures, sells and installs MagneGrip Exhaust Removal Systems, AirHAWK Air Purification Systems and HazVent Pneumatic Exhaust Removal Systems. Continuously improved and modified, MagneGrip systems have been installed in thousands of locations through a nationwide and global distribution and service network. MagneGrip is ISO 9001:2015 Certified and ‘Made in the USA’.
Diesel exhaust emissions can spread toxic gases and soot particles throughout a firehouse anytime a diesel-fueled engine is operated. When diesel fuel is burned, it produces polycyclic aromatic hydrocarbons and diesel soot. Both of these substances are classified as carcinogens. Ultrafine particulate can penetrate deep into the lung and is absorbed through the skin, carrying toxins into the bloodstream. Exposure to this type of pollution can increase the risk for developing cancer, and respiratory and cardiovascular diseases. The World Health Organization’s classification of diesel exhaust emissions as “carcinogenic to humans,” is hardly a surprise. Numerous studies have been coming to the same conclusion for several years. Medical studies point to firefighters’ higher rates for several cancers and other debilitating diseases than the general public for confirming evidence of this workplace hazard. Studies also led the National Institute for Occupational Safety and Health (NIOSH) and the Environmental Protection Agency (EPA) to conclude that diesel exhaust most likely causes cancer. In addition, the National Fire Protection Agency (NFPA) in its 1500 standard “advocates the need for the elimination and containment of all vehicle exhaust emissions to a level of no less that 100% effective capture.” Providing adequate protection Several types of exhaust removal systems are marketed to the fire services. Many of them are inadequate because they remove only a portion of the toxic contaminants. Those solutions that consist of fans and air vents do very little to reduce exposure to the hazardous toxins. Likewise, filtration systems mounted above vehicles obviously do not capture all the exhaust emissions and some of the harmful gases and particulates are able to spread throughout the firehouse. The International Mechanical Code for new construction specifically states: “Areas in which stationary motor vehicles are operated shall be provided with a source capture system that connects directly to the motor vehicle exhaust system.” Under-body devices that replace a vehicle’s muffler, are inadequate because they only “filter”—and do not “eliminate”—the exhaust emissions. Such attachments filter out some of the solid substances, but not the gaseous toxins released into the air. These devices may reduce the appearance of smoke, but the harmful gases in diesel exhaust such as CO (carbon monoxide), VOCs (volatile organic compounds), and HC (hydrocarbon) are invisible . . . but deadly. In addition, muffler replacement equipment requires frequent and costly filter cleaning or replacement. The diesel particulate filter (DPF), which is required on newer model apparatus, removes large particulate but not sub-micron particulate or gaseous substance. And significantly more fine particles are produced with newer diesel engines. In today’s market, only a few manufacturers can make valid claims for removing exhaust emissions from the firehouse. However, not all of these systems are created equal. Some are complicated in design and not user-friendly, and some require extra attachments and equipment to operate. What makes better technology? One of the most important innovations in exhaust removal design was developed by MagneGrip Group to eliminate problems with traditional exhaust removal systems. Its patented universal nozzle uses rare-earth magnet assemblies to support the nozzle’s connection to the apparatus tailpipe. This design eliminates the need for compressors, air lines, gauges, safety disconnect components, and electrical system support. This makes the system safer and easier to use than any other source-capture system. It also requires the least maintenance of any system. MagneGrip offers the only no-leak sealed system that allows outside air to enter the nozzle chamber. A one-way check valve enables air to enter, but seals against exhaust fume backwash. Outside air mixing with the exhaust provides cooler nozzle and hose operation and less wear. It also reduces negative air pressure on the apparatus turbocharger when the engine is not running, and avoids damage from the turbocharger spinning without lubrication. Operation is fully automatic and does not reduce response time. On emergency runs, the nozzle remains attached until the apparatus tailpipe reaches the doorway; then it automatically releases. The nozzle disconnects easily and smoothly, and a cable gently retracts the hose and nozzle away from the exit. MagneGrip systems have been proven in thousands of installations nationwide. Today, they are the first choice of U.S. fire departments. This acceptance affirms the reliability of MagneGrip’s service and its systems’ components, which are built to provide many years of dependable service. A system for every firehouse MagneGrip has more exhaust removal solutions than any other company. Since buildings, apparatus configurations and operations vary, it is important to have the right system to meet the specific needs of every firehouse. MagneGrip systems include: 1.) Sliding Flexhose Track (SFT) System – A compact system that works well in firehouses with back-in bays that have low ceilings or narrow spaces between vehicles. Only 16-21 inch aisles are needed. This streamlined system has no hanging hose loops. 2.) Sliding Balancer Track (SBT) System – A good choice for drive-thru bays, providing door-to-door exhaust capture. The system can be installed in each bay for one vehicle or two vehicles parked in tandem, and it connects to emergency or non-emergency vehicles. 3.) Straight Suction Rail (SSR) System – This system is ideal for firehouses with little room to spare. It accommodates up to four emergency response vehicles parked in tandem. The SSR system uses the MagneGrip nozzle and minimum hose lengths. 4.) Vertical Stack Rail (VSR) System – Designed for vehicles with a vertical exhaust stack. No manual connection is required. When the apparatus returns from a run and enters the station, the stack catcher automatically adjusts to align the suction rail with the exhaust stack. 5.) Simple Drop System – It has the same components as the SBT system, without the track. On emergency runs, the nozzle remains connected until the hose and cable are fully extended and then it automatically releases. An economical option for vehicles that may be started daily, but are not used regularly for emergency runs. Recent design advances MagneGrip continues to innovate and bring new design enhancements to its exhaust removal systems: Wireless Transmitters are used to automatically start the exhaust fan before the engine starts and prior to the apparatus reentering the facility. This eliminates the escape of exhaust fume in the building. MagneGrip Exhaust Fans are designed solely for exhaust removal. Spark-resistant, curved blades deliver the highest efficiency, and the fans run quieter than conventional fans. The die-stamped Lifting Elbow on MagneGrip systems eliminates hose pinch, twisting and sliding that occur with old-style rubber saddles. From the lifting elbow to the nozzle, a Support Cable inside the hose bears the weight to eliminate hose stretching. It also ensures easy release of the nozzle. The lower two feet of the MagneGrip hose is 5-ply thickness for rugged durability. An attached handle makes connecting the system effortless from a standing position. GREEN OPTION – MagneGrip offers an Inline Particulate Filter, which can be positioned in the system’s ductwork, to capture exhaust particulates so they are not expelled into the air outside. For more than 15 years, MagneGrip has led the exhaust removal industry with major advances in technology and design. And . . . MagneGrip systems are professionally installed by a nationwide team of service technicians to provide guaranteed satisfaction. Made in America MagneGrip Exhaust Removal Systems are completely (100 percent) manufactured in the U.S.A. Firefighters and EMTs can take pride in having a system that is “All American,” as well as the safest, most efficient system available. Competitive systems are often the products of foreign companies, which are largely manufactured outside the U.S. MagneGrip uses American Standard parts (not metric), so if any adjustment or repairs are needed, most departments will already have the tools on hand. For more information, a proposal, grant assistance or budgetary numbers, visit www.magnegrip.com, email info@magnegrip.com, or call 800-875-5440. A full-color brochure and a video DVD demonstrating the advantages of MagneGrip systems are available. Print Story: Clearing the Air – FireRescue1.com Revised June 25, 2014
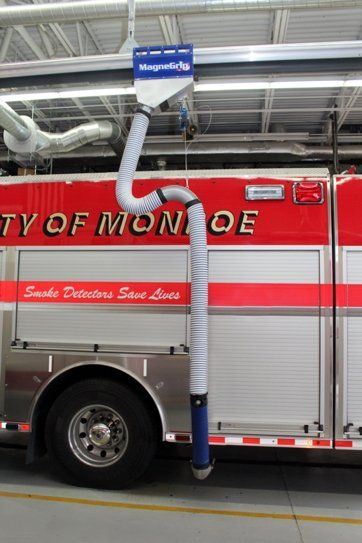
Monroe Fire Department in Monroe, Ohio has taken a proactive approach to cancer prevention and to ensuring the health and well-being of their fire fighters. A top priority in that goal was the installation of a MagneGrip Exhaust Removal System. Working with Assistant Chief Dave Leverage, MagneGrip installed an exhaust removal system. MagneGrip Exhaust Removal Systems remove diesel exhaust emissions in firehouses to reduce firefighter risk for cancer, respiratory and cardiovascular diseases. The patented magnetic nozzle provides an airtight seal and is 100% effective in removing exhaust emissions. Systems have wireless auto-start activation. MagneGrip’s 1,000° F rated hose is now standard equipment. In the video , Chief Leverage notes the importance of exhaust removal in the health and safety of Monroe Fire Department’s fire fighters and the ease of working with MagneGrip to install an effective and efficient system to reduce first responders' cancer risk.
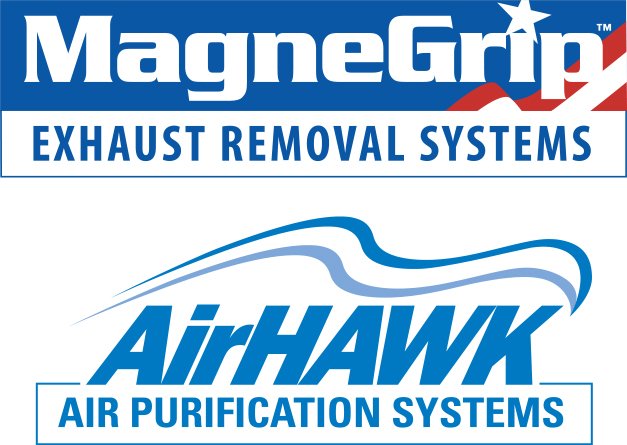
MagneGrip Group is exhibiting at two conferences in August 2019: Fire-Rescue International (FRI) in Atlanta, GA August 9-11 and South Atlantic Fire Rescue Expo (SAFRE) in Raleigh, NC August 23-23. MagneGrip Exhaust Removal Systems and AirHAWK Air Purification Systems products will be on display in booth 1323 at FRI and in booth 421 at SAFRE. Sales Representatives will be available to answer questions and demonstrate product features during both conferences.MagneGrip Group manufactures air-cleaning systems for every firehouse application to eliminate exhaust fumes and other airborne contaminants that pose critical health risks. MagneGrip Exhaust Removal Systems and AirHAWK Air Purification Systems are suitable for every firehouse application; they can be used separately or combined, for the most effective protection possible. For more information and a budgetary proposal call MagneGrip at 800-875-5440, email info@magnegrip.com or visit www.magnegrip.com.
MagneGrip Exhaust Removal Systems, there is nothing more effective at removing toxic air contaminantsMagneGrip offers systems designed to eliminate hazardous exhaust emissionsCompany Name: MagneGrip Group (A Division of Clean Air Concepts)Headquarters: Cincinnati, OHSignature Products: MagneGrip Sliding Flexhose Track (SFT) and AirHAWK 3000 XLWebsite: www.magnegrip.com1) Where did your company name originate?The company name, MagneGrip Group (A Division of Clean Air Concepts) originated from MagneGrip Exhaust Removal System’s magnetic nozzle technology. Rare-earth magnet assemblies provide the holding power needed to connect the exhaust removal nozzle to the tailpipe until it automatically releases when the vehicle exits a building. MagneGrip Exhaust Removal System’s source capture nozzle design does not rely on electric wiring, air lines or gauges to disconnect; and there are no attachments to the side of the apparatus.Ed Rossman founded the company in 1975 to provide air purification equipment and exhaust removal systems. Based in Cincinnati, Ohio, MagneGrip Group manufactures the #1-rated solution to the health threat of diesel exhaust emissions in firehouses and vehicle maintenance facilities. 2) What was the inspiration behind starting the company?As an answer to the health threat of diesel exhaust emissions in firehouses and vehicle maintenance facilities,MagneGrip Group was started to provide a better, more cost-effective and easier to use source capture system. 3) What is your signature product and how does it work?There are two signature products: MagneGrip Sliding Flexhose Track (SFT) and AirHAWK 3000 XL.MagneGrip Sliding Flexhose Track (SFT) is the most compact source-capture system available. It is the ideal system for firehouses with back-in bays that have low ceilings or narrow spaces between vehicles—needing only 19-24 inch aisles. The SFT system has no hanging hose loops that block access to doors or loading. An auto-start sensor activates the exhaust fan as the apparatus operator starts the engine. The airtight expandable flexhose extends along the track as the apparatus moves forward. The nozzle remains attached until it automatically releases at the threshold of the door. The SFT system is 100 percent sealed so no toxic exhaust fumes escape into the firehouse. When the apparatus enters the firehouse, an automatic activation device starts the exhaust fan. The nozzle is connected and the apparatus is backed into the bay. MagneGrip systems have the highest airflow in any 100 percent sealed system. This totally removes exhaust emissions in the fastest, most effective manner possible.Sliding Balancer Track (SBT), Straight Suction Rail (SSR) and Vertical Stack Rail (VSR) are other exhaust removal systems in the MagneGrip product line. AirHAWK Air Purification Systems clean air as it is being generated, providing continuous air purification and coverage for an entire area or facility. It also meets OHSA guidelines and is easy to use with no firefighter involvement. AirHAWK Air Purification Systems utilize a four-stage filtration process to destroy toxic organic compounds, which is why its air cleaning and purification performance is superior to all other systems. AirHAWK'S unit placement and design of the air circulation pattern are also critical to air purification and circulation effectiveness. 4) Why are your products essential to the Fire and EMS community?Apparatus in fire stations discharge diesel exhaust into the breathing area. Exposure to toxic gases and particulate is linked to cancer and other debilitating diseases. As a result, fire and EMS personnel have an increased risk of cancer-causing deaths than the general population. To reduce the risk of cancer, MagneGrip Exhaust Removal Systems connect directly to the vehicle tailpipe to remove contaminants and protect first responders. AirHAWK ceiling-mounted filtration units capture engine exhaust emissions and off-gases in firehouses. With cutting-edge technology such as photo-catalytic oxidation, airborne toxins are removed. 5) What has been the biggest challenge your company has faced?Supporting firefighter cancer awareness and cancer risk avoidance are the biggest challenges MagneGrip Group faces everyday. 6) What makes your company unique? MagneGrip Group is an American company, family owned and operated in Cincinnati, Ohio. All products are made in the USA and installed through a national and global distribution and service network. MagneGrip Group is ISO 9001:2015 Certified. We are proud to work with fire departments with one station or as many as 100 stations. 7) What do your customers like best about you and your products?One of our customers said it best: "The biggest benefit of the MagneGrip System is the ease of use. The hose snaps on to the MagneGrip tailpipe adaptor with magnets; the auto sensors turn the blowers on when the apparatus is started to begin exhaust removal. It's quick and easy to use. And for the health of our firefighters, it's reassuring to know we are reducing the risk and worry of diseases caused by diesel exhaust." MagneGrip Exhaust Removal System’s direct source-capture system is the best protection available. MagneGrip systems meet the NFPA 1500 Standard for “no less than 100 percent effective capture” to eliminate dangerous exhaust emissions in firehouses. 8) What is the most rewarding part of serving the first responder community?Knowing that our products keep fire and EMS staff from the harmful effects of diesel exhaust and particulates is the most rewarding part of serving the first responder community. What motivates us everyday is providing a clean firehouse environment for emergency personnel who encounter daily job hazards. 9) Do you support any charitable organizations within the public safety community? The Fire Fighter Cancer Foundation and MagneGrip Group have formed a partnership to help extinguish fire fighter cancer. The Foundation provides education to alert fire fighters to the cancer-causing exposures in their occupation and it advocates for cancer research and presumptive legislation. It also helps active and retired fire fighters who have cancer with resource information and assistance during treatment. With support from MagneGrip Group, the Foundation is able to provide the latest information on protecting fire fighter health in the firehouse. Diesel exhaust particulate and gases are known carcinogens and, if not eliminated, exposure to these toxins can cause debilitating illnesses.MagneGrip Group furnishes AirHAWK 265 units to the Fire Fighter Cancer Foundation at reduced cost for cancer victims in need. The portable AH 265 units provide air purification and germicidal protection.10) Is there any fun fact you’d like to share about the company?MagneGrip Group’s founder, Ed Rossman, originally began working in the air purification and exhaust removal industry with a competitor. His objective in establishing the MagneGrip Group was a simpler, better way to manufacture and distribute exhaust removal and air purification systems to fire, EMS and vehicle maintenance facilities.11) What’s next for your company? Any upcoming new projects? We are continuously working to improve and modify our products. As an example, to withstand higher vehicle exhaust temperatures, the lower two feet of hose was modified. It is rated to withstand up to 1,000° F. This feature is standard on all MagneGrip hoses. https://www.firerescue1.com/fire-products/apparatus-accessories/articles/393418018-Spotlight-MagneGrip-Exhaust-Removal-Systems-there-is-nothing-more-effective-at-removing-toxic-air-contaminants/
Cincinnati, Ohio – MagneGrip announced that Maggie Rossman-Roach has been appointed President. In addition, Jack Rossman has been named Chief Operating Officer and Tom Rossman is Chief Logistics Officer. These leadership appointments follow the loss of founder and president, Edward J. Rossman in August 2018. Ms. Rossman-Roach had been Vice President and Controller before succeeding her father as president. The senior leadership team has over 60 years of experience in the air purification and exhaust removal industry. “I am proud to continue the legacy started by my father, Ed Rossman and his commitment to breathing clean air,” said Rossman-Roach. “We are grateful to our customers for their business. Our pledge is to continue the growth of the company, to reduce the risk of cancer in firehouses and vehicle maintenance facilities and expand our presence even further than it is today. With our team of highly experienced and customer-focused sales representatives, distributors, technicians and office staff, business has never been better and the future has never looked brighter.”About MagneGrip was founded in 1975 to provide air purification equipment and exhaust removal systems. Based in Cincinnati, Ohio, MagneGrip manufactures the #1-rated solution to the health threat of diesel exhaust emissions in firehouses and vehicle maintenance facilities. MagneGrip engineers, manufactures, sells and installs MagneGrip Exhaust Removal Systems, AirHAWK Air Purification Systems and HazVent Pneumatic Exhaust Removal Systems. Continuously improved and modified, MagneGrip systems have been installed in thousands of locations through a nationwide and global distribution and service network. MagneGrip is ISO 9001:2015 Certified and ‘Made in the USA’.
Firefighter cancer is a looming personal catastrophe for each and every fire fighter and is the most dangerous threat to the health and safety of our nation’s firefighters. Cancer has caused 61% of career firefighter line-of-duty deaths sine 2001. By contrast, heart disease has caused 18% of line-of-duty deaths during the same time period. (IAFF data Jan. 1, 2002 to March 31, 2017.) Multiple studies, including the 2010 NIOSH cancer study, have repeatedly demonstrated credible evidence for statistically higher rates of multiple types of cancers in firefighters compared to the general American population including:• Testicular cancer (2.02 times greater risk)• Mesothelioma (2.0 times greater risk)• Multiple myeloma (1.53 times greater risk)• Non-Hodgkin’s lymphoma (1.51 times greater risk)• Skin cancer (1.39 times greater risk)• Prostate cancer (1.28 times greater risk)• Malignant melanoma (1.31 times great risk)• Brain cancer (1.31 times greater risk)• Colon cancer (1.21 times great risk)• Leukemia (1.14 times greater risk)• Breast cancer in women (preliminary study results from the San Francisco Fire Department) We are beginning to understand the horrific magnitude of the problem, the challenges involved and the changes required in education, training, operations, medical screenings and personal accountability to effectively address cancer in the fire service.Yet, the signs of firefighters’ exposure to carcinogens are everywhere:• Firefighters working in active and overhaul fire environments carry SCBA on their backs but not always masks on their faces.• Firefighters proudly wear dirty and contaminated turnout gear and helmets.• Some fire instructors wear their carcinogen-loaded helmets and bunker gear as symbols of their firefighting experience. • Diesel exhaust, a recognized carcinogen, still contaminates many fire stations— apparatus bays as well as living, sleeping and eating quarters. • Many firefighters have only one set of gear, which means they are continually re-contaminated from previous fires.• Some diesel exhaust systems — even when installed — are not used, are used incorrectly or are poorly maintained.• Bunker gear is stored in apparatus bays where it is bathed in diesel exhaust.• Bunker gear goes unwashed for months at a time, even after significant fires. • Many volunteers carry their contaminated gear in the trunks of their personal vehicles resulting in superheating and enhanced off-gassing of contaminants into the passenger compartment and sometimes even into their homes. • Firefighters put their contaminated gear into the cabs of their apparatus before and after fires.• Some firefighters still take their contaminated bunker pants and boots into sleeping quarters.• The interiors of apparatus cabs are not decontaminated adequately or frequently.• Many firefighters do not take showers immediately following fires. “Pinpointing the cause of cancer is extremely difficult because firefighters are not exposed to just one agent. They are exposed to multiple cancer-causing agents. Because of the multiple exposures and the multiple routes of exposure — they inhale carcinogens and carcinogens are absorbed through the skin — it is also highly unlikely for firefighters to get only one type of cancer,” said Grace LeMasters, Ph.D., a professor of epidemiology at the University of Cincinnati and the lead author of a 2006 meta-analysis of 32 published studies of cancer in firefighters. Unfortunately, there is no immediate visible impact of carcinogenic exposure, since the time between exposure to carcinogens and the appearance of malignancies can be 20 years or longer. However, a large multi-institution multi-fire department study is underway to closely track firefighter occupational exposures and health effects. The study will establish the most meaningful correlations yet between firefighting and cancer. MagneGrip Exhaust Removal Systems reduce firefighter risk for cancer, respiratory and cardiovascular diseases by removing diesel exhaust emissions in the firehouses. With AirHawk Air Purification Systems, ceiling-mounted air filtration units remove hazardous airborne contaminants including viruses, bacteria and mold spores and neutralize gaseous compounds such as carbon monoxide and nitrous oxide. For information, call 800-875-5440 or visit www.magnegrip.com. Excerpts from: Firefighter Cancer Support Network white paper, “Firefighter Cancer Fact Check 2017”, Timothy Elliott and Fire Chief “Command Post,” weekly e-news, August 22, 2013.
Share On: